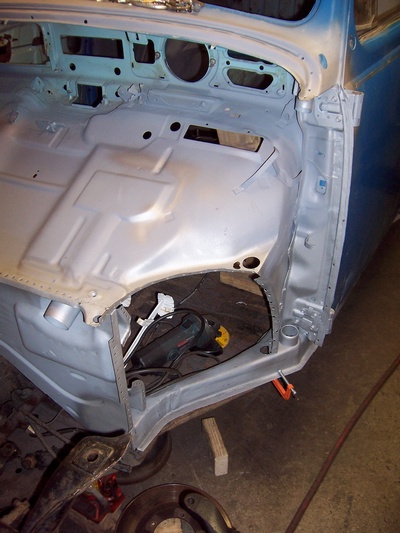
This section has been sand blasted and primed with weldable primer. Just about ready to weld in the quarter panel.
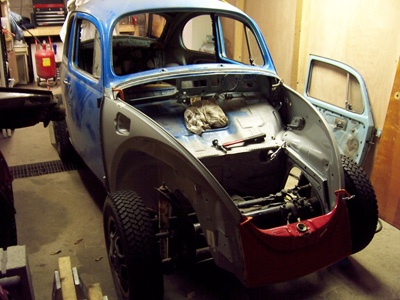
The final mock up of the two quarter panels and the front clip. Everything is lining up pretty good. I will attempt to keep everything as straight as I can as I start to tack everything in.

The start of the spot welds! I drilled holes into the quarter panel, and welded each one up. It was important to weld each time in a completely different area so the heat would not build up and warp the panel. The edge were the drip rail and panel come together (In front of the door) will be a tricky area to perfect. I have to bend the outside edge around to the front. I will carefully grind the welds down first.
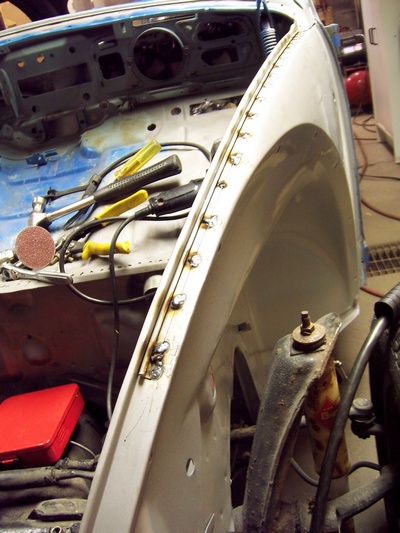
Here I've tacked on the weather strip holding piece. This metal is a bit thinner then the rest of the car, so I had to go quickly to not burn through. My first side I had drilled holes through the strip, and welded them up, but I found that this was too aggressive. The other side I ended up just welding spots directly beside the strip, and moving in on the strip. This gave a much cleaner weld, and actually burned through much less. After welding, I went through and ground down the top and bottom of each weld.
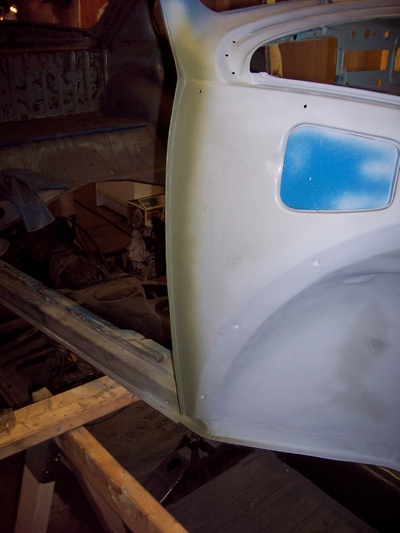
Here is the right side after grinding the welds down, bending the edge over, and hammer / dollying the crap out of it for a while. Turned out pretty good. Any section that was bulging out a bit, I hit with a flat file. Later when I'm doing paint prep, I may revisit this area and make sure this line is very smooth and straight. Maybe a little bondo (and paint, make it what it aint! :)
Labels: build up, metal work