41) Alternator Bracket
With the rotated coolant manifold the stock location of the alternator no longer works. Slowly, I built up a bracket that would bolt into the location of the old power steering pump. I mostly used 3/4" square tubing, with a few pieces of spare metal that I had laying around also. (There are some pieces of old bumper brackets and bed frame angle iron in there :)

This is the pivot side of the alternator. I needed to make sure the oil pressure sensor and throttle body preheater hose would fit around the bracket.

This is a mock up of the adjustable side of the alternator. The OEM bracket bolts from the other side, but I'm planning to bolt through in this direction because it is less fabricating and material needed.
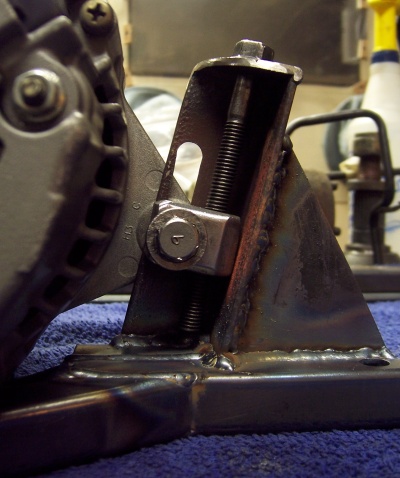
This is the front side of the adjuster. You can see here it adjusts like normal, just from the other side. I had to pay a lot of attention to the min and max adjustments of the alternator to be able to get the most travel possible. I ended up having to grind down the intake and alternator a bit to get even more travel.
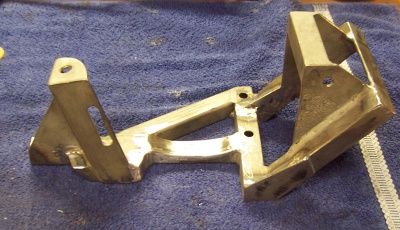
This is the roughly finished bracket (minus paint of course). I added some gusseting to make a little more rigid.
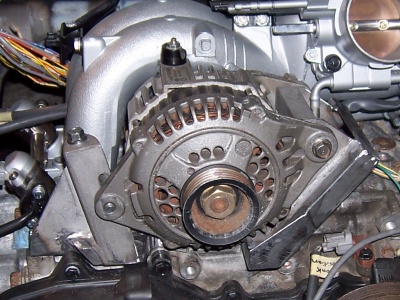
Finished and alternator mocked up. Next up will be to find a belt that fits!
Labels: engine, metal work